在3D打印技術(shù)高速發(fā)展的今天,金屬粉末作為增材制造的核心原材料,其性能直接決定了打印件的機(jī)械強(qiáng)度、表面精度和內(nèi)部缺陷率。金屬粉末的粒度分布、顆粒形貌、流動(dòng)性等參數(shù),不僅影響鋪粉均勻性和激光熔化效率,還關(guān)系到最終產(chǎn)品的疲勞壽命與耐腐蝕性。例如,在航空航天領(lǐng)域,鈦合金粉末的D90值若超出53μm,可能導(dǎo)致熔池能量吸收不足,打印層間結(jié)合力下降;而衛(wèi)星粉(附著于主顆粒表面的微細(xì)顆粒)過(guò)多則會(huì)降低粉末流動(dòng)性,引發(fā)鋪粉不均甚至噴頭堵塞。傳統(tǒng)的篩分法、顯微鏡觀察等手段已無(wú)法滿足現(xiàn)代3D打印工業(yè)對(duì)高效、精準(zhǔn)、可重復(fù)的檢測(cè)需求,激光粒度儀憑借其非接觸式測(cè)量、寬動(dòng)態(tài)范圍(0.02-2600μm)及智能數(shù)據(jù)分析能力,正在成為金屬粉末質(zhì)量控制與工藝優(yōu)化的核心工具。
作為粒度分析技術(shù)的重要推動(dòng)者,百特激光粒度儀通過(guò)模塊化光路設(shè)計(jì)、多物理場(chǎng)耦合算法及工業(yè)場(chǎng)景適應(yīng)性創(chuàng)新,為3D打印行業(yè)提供了從原材料篩選到在線生產(chǎn)的全流程解決方案。本文將從金屬粉末特性、增材制造工藝需求及設(shè)備技術(shù)突破三個(gè)維度,系統(tǒng)解析激光粒度儀在3D打印中的關(guān)鍵作用,并結(jié)合實(shí)際應(yīng)用案例,展現(xiàn)其在提升打印質(zhì)量與生產(chǎn)效率中的工程價(jià)值。
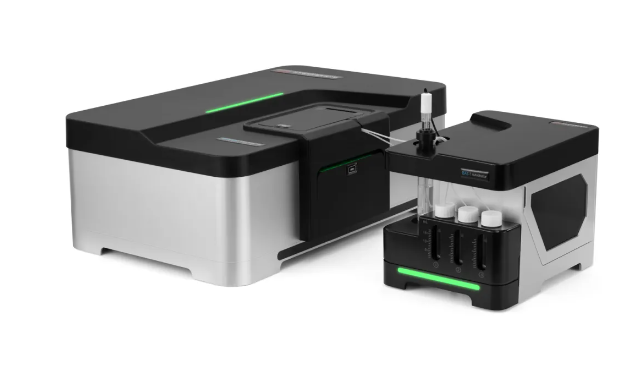
一、3D打印金屬粉末的粒度控制要求與行業(yè)痛點(diǎn)
金屬粉末的粒度分布是影響3D打印質(zhì)量的核心參數(shù)。研究表明,粉末的D50值需控制在20-45μm范圍內(nèi)以確保鋪粉層厚均勻性,而跨距值(Span=(D90-D10)/D50)與打印件抗拉強(qiáng)度呈顯著負(fù)相關(guān),跨距每增加0.2,強(qiáng)度下降8%-12%。然而,當(dāng)前行業(yè)面臨以下挑戰(zhàn):
多批次一致性差:氣霧化粉末的D50波動(dòng)超過(guò)±3μm時(shí),打印參數(shù)需頻繁調(diào)整,良品率降低15%-20%;
衛(wèi)星粉干擾:衛(wèi)星粉占比超過(guò)0.5%會(huì)顯著降低粉末流動(dòng)性,導(dǎo)致鋪粉不均和粉塵污染;
高溫在線監(jiān)測(cè)缺失:傳統(tǒng)實(shí)驗(yàn)室檢測(cè)耗時(shí)長(zhǎng)達(dá)2-4小時(shí),無(wú)法實(shí)時(shí)反饋產(chǎn)線狀態(tài)。
針對(duì)這些問(wèn)題,百特激光粒度儀通過(guò)高分辨率檢測(cè)技術(shù)與智能算法,實(shí)現(xiàn)了對(duì)粉末特性的精準(zhǔn)把控。例如,百特Bettersize2600采用正反傅里葉結(jié)合傾斜樣品池光路技術(shù),覆蓋0.02-2600μm測(cè)量范圍,其干法分散模塊通過(guò)氣壓閉環(huán)控制,可精準(zhǔn)捕捉主顆粒與衛(wèi)星粉的獨(dú)立分布曲線,重復(fù)性誤差≤0.5%。某航空航天企業(yè)引入該設(shè)備后,粉末批次一致性偏差從±8%降至±2%,打印件疲勞壽命提升30%。
二、激光粒度儀在3D打印中的核心應(yīng)用場(chǎng)景
1. 金屬粉末原料質(zhì)量控制
在金屬粉末生產(chǎn)環(huán)節(jié),百特BT-Online1A在線粒度儀集成至霧化塔出口管路,通過(guò)OPC UA協(xié)議與PLC系統(tǒng)直連,實(shí)現(xiàn)實(shí)時(shí)預(yù)警與參數(shù)自整定。當(dāng)檢測(cè)到D50值偏離設(shè)定閾值±2μm時(shí),系統(tǒng)自動(dòng)調(diào)節(jié)霧化氣壓與轉(zhuǎn)速,將粉末回收率從65%提升至85%。該設(shè)備的氮?dú)庹龎悍雷o(hù)倉(cāng)和三溫區(qū)PID溫控系統(tǒng),可在40-60℃的高溫高濕環(huán)境中穩(wěn)定運(yùn)行,光路溫漂控制在±0.01℃/h。
2. 多組分復(fù)合粉末分析
對(duì)于WC-Co金屬陶瓷粉末,百特Bettersize3000Plus激光/圖像聯(lián)合分析儀采用532nm/635nm雙波長(zhǎng)激光與Mie-Fraunhofer復(fù)合算法,同步解析WC硬質(zhì)相(2-10μm)與Co粘結(jié)相(0.5-2μm)的分布特征。其動(dòng)態(tài)圖像分析技術(shù)可捕捉顆粒長(zhǎng)徑比、圓形度等形貌參數(shù),為優(yōu)化粉末流動(dòng)性與燒結(jié)致密性提供數(shù)據(jù)支持。某醫(yī)療植入物生產(chǎn)企業(yè)通過(guò)該設(shè)備建立D10>15μm、Span<1.2的質(zhì)量標(biāo)準(zhǔn),生物相容性測(cè)試通過(guò)率從82%提升至98%。
3. 粉末回收工藝優(yōu)化
在多次循環(huán)使用的316L不銹鋼粉檢測(cè)中,百特BT-9300SE激光粒度儀通過(guò)XD陣列檢測(cè)器與PIDS偏振光差分技術(shù),識(shí)別0.1μm級(jí)衛(wèi)星粉并消除假峰干擾。結(jié)合ADAPT多峰自動(dòng)識(shí)別軟件,設(shè)備可分離金屬粉末主峰、衛(wèi)星粉次峰及團(tuán)聚體干擾峰,為篩分參數(shù)調(diào)整提供依據(jù)。
三、技術(shù)突破與行業(yè)實(shí)踐
1. 高分辨率與抗干擾能力
百特開(kāi)發(fā)的多通道光電探測(cè)器陣列與雙偏振光散射技術(shù),解決了細(xì)顆粒端信號(hào)采集靈敏度不足的行業(yè)難題。例如,在鈦合金粉末檢測(cè)中,該技術(shù)可區(qū)分粘附顆粒與獨(dú)立細(xì)粉,避免傳統(tǒng)激光粒度儀因分辨率不足導(dǎo)致的衛(wèi)星粉漏檢問(wèn)題。
2. 智能化數(shù)據(jù)融合
ADAPT軟件基于深度學(xué)習(xí)框架,支持與SEM、XRD等設(shè)備數(shù)據(jù)聯(lián)動(dòng),建立粒度-形貌-成分多維關(guān)聯(lián)模型。某新能源車企利用該功能優(yōu)化鋁硅合金粉末配方,將打印件抗拉強(qiáng)度從285MPa提升至320MPa,鋪粉層厚標(biāo)準(zhǔn)偏差從4.7%降至1.2%。
四、未來(lái)發(fā)展趨勢(shì)
超高速在線檢測(cè):百特正在研發(fā)μs級(jí)采樣技術(shù),可實(shí)時(shí)捕捉霧化塔內(nèi)粉末生成動(dòng)態(tài),同步分析粒度-形貌-溫度多參數(shù);
數(shù)字孿生集成:通過(guò)將粒度數(shù)據(jù)導(dǎo)入增材制造數(shù)字孿生平臺(tái),預(yù)測(cè)不同分布下的熔池流動(dòng)與結(jié)晶行為;
AI驅(qū)動(dòng)逆向優(yōu)化:基于打印件力學(xué)性能數(shù)據(jù),反向推薦最佳粒度分布區(qū)間,實(shí)現(xiàn)工藝參數(shù)自動(dòng)調(diào)優(yōu)。
結(jié)語(yǔ)
從粉末霧化的微觀世界到航空發(fā)動(dòng)機(jī)葉片的宏觀性能,激光粒度儀正在重新定義3D打印質(zhì)量控制的邊界。百特通過(guò)持續(xù)的技術(shù)迭代,將實(shí)驗(yàn)室級(jí)精度融入工業(yè)生產(chǎn)線,幫助客戶在成本與品質(zhì)之間找到最優(yōu)解。未來(lái),隨著人工智能與量子傳感技術(shù)的突破,粒度分析將從單一參數(shù)檢測(cè)升級(jí)為工藝優(yōu)化的核心驅(qū)動(dòng)引擎,而具備多維度數(shù)據(jù)融合能力的智能粒度儀,必將成為增材制造智能化進(jìn)程中不可或缺的“質(zhì)量守門人”。